تجهیزات آماده سازی و دوز پلی الکترولیت از سیستم های اتوماسیون ویسکوزیته خطی استفاده می کنند
تصفیه خانه ها با چالش قوانین سختگیرانه و استانداردهای بالاتر برای کیفیت آب تمام شده مواجه هستند. پیشرفت های جدید در استراتژی های کنترل و طراحی ابزار بر برخی از محدودیت های قبلی نظارت و کنترل فرآیند انعقاد غلبه کرده است. یک تحلیلگر لخته آنلاین اطلاعات ارزشمندی در مورد پویایی تجمع ذرات پس از انعقاد ارائه می دهد.
بهینه سازی انعقاد لخته ای را تشکیل می دهد که بزرگ است و به راحتی ته نشین می شود. تجزیه و تحلیل فراکتال نشان داده است که انتشار و برخورد ذرات کلوئیدی تجمع ذرات را محدود می کند. بنابراین، اختلاط مناسب یک عامل اصلی موثر بر تشکیل لخته است.
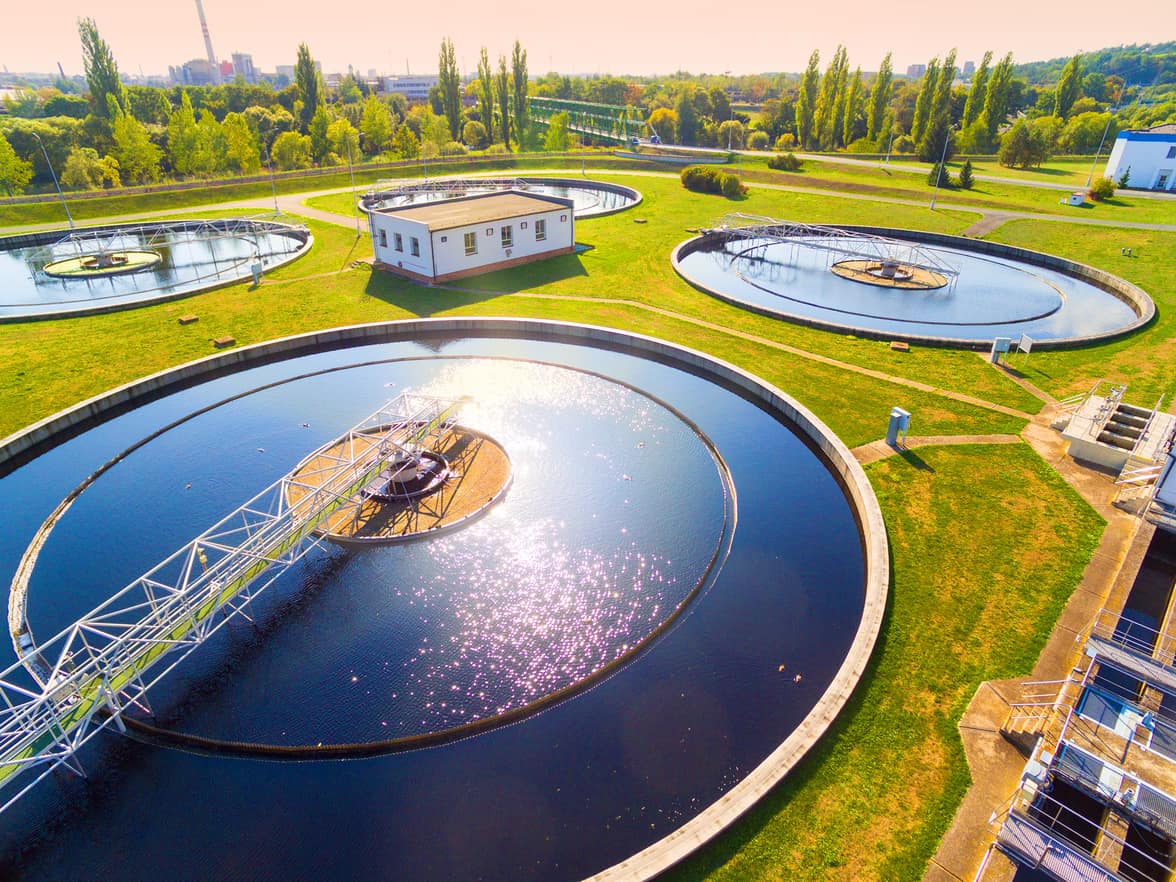
کاربرد
انعقاد یک فرآیند ضروری برای حذف مواد معلق و کلوئیدی از آب و فاضلاب است. لخته سازی درون خطی یک تکنیک امیدوارکننده برای آبگیری و اصلاح باطله ماسه های نفتی است.
- برای تمیز کردن پساب صنعت و بازیافت آن برای استفاده بیشتر
- کاهش مصرف آب شیرین و آشامیدنی در صنایع
- کاهش هزینه های تامین آب
- رعایت استانداردهای انتشار یا تخلیه آلاینده های زیست محیطی از صنایع مختلف که توسط دولت تعیین شده است و اجتناب از جریمه های سنگین
- حفاظت از محیط زیست در برابر آلودگی و کمک به توسعه پایدار
لخته سازی چیست؟
لخته سازی یک فرآیند تصفیه آب است که در آن مواد جامد خوشه های بزرگتر یا لخته ها را تشکیل می دهند تا از آب حذف شوند. این فرآیند می تواند خود به خود یا با کمک عوامل شیمیایی اتفاق بیفتد. این یک روش متداول برای تصفیه آب طوفان، تصفیه فاضلاب و در تصفیه آب آشامیدنی است. یکی از الزامات خروج آب تصفیه شده از کارخانه های فاضلاب، حذف مواد معلق است. ذرات جامد کوچک بر رنگ آب تأثیر میگذارند و ناخالصیها را به منابع آب طبیعی ما مانند رودخانهها و اقیانوسها منتقل میکنند.
انعقاد و لخته سازی یک سوسپانسیون کلوئیدی پس از افزودن یک سیستم منعقد کننده-لخته ساز پس از اختلاط با ته نشین شدن بعدی شبکه لخته
فلوکولانت ها چیست؟
فلوکولانت ها ترکیباتی هستند که تجمع ذرات ریز را در یک محلول تحریک می کنند و در نتیجه یک لخته تشکیل می شود که متعاقباً به سمت بالا شناور می شود (فلوتاسیون) یا به پایین فرو می رود (رسوب). علاوه بر این، ممکن است این ماده با سهولت بیشتری از مایع استخراج شود. لخته های معدنی و آلی در انواع بارها، وزن مولکولی، چگالی بار و مورفولوژی موجود هستند.
عواقب غلظت نادرست فاضلاب
تصفیه خانه ها با چالش قوانین سختگیرانه و استانداردهای بالاتر برای کیفیت آب تمام شده مواجه هستند.
بدون تمرکز مناسب، موارد زیر وجود دارد:
- احتمال شکست فاجعه بار
- تاسیسات تصفیه مسدود شده (فاضلاب)
- لوله های یخ زده، ترکید
- تصفیه نامناسب آب
- آب تصفیه شده نادرست تخلیه می شود که منجر به جریمه بالا می شود
پیشرفت های جدید در استراتژی های کنترل و طراحی ابزار بر برخی از محدودیت های قبلی نظارت و کنترل فرآیند انعقاد غلبه کرده است. یک تحلیلگر لخته آنلاین اطلاعات ارزشمندی در مورد پویایی تجمع ذرات پس از انعقاد ارائه می دهد.
بهینه سازی انعقاد لخته ای را تشکیل می دهد که بزرگ است و به راحتی ته نشین می شود. تجزیه و تحلیل فراکتال نشان داده است که انتشار و برخورد ذرات کلوئیدی تجمع ذرات را محدود می کند. بنابراین، اختلاط مناسب یک عامل اصلی موثر بر تشکیل لخته است.
صنایع:
نیروگاه، فولاد، پالایشگاه، معدن، مواد غذایی، شکر، تقطیر، الکترونیک، کود، مواد شیمیایی، نساجی، کاغذ و خمیر، سیمان، مهمان نوازی، تجاری، مسکونی
برنامه های کاربردی:
- شفاف سازی آب خام
- حذف رنگ
- آبگیری لجن
- روغن زدایی
- کاربردهای فرآیند صنعتی
برای اینکه تاسیسات تصفیه زباله با مقررات سختگیرانهتر مطابقت داشته باشند و ایمن و کارآمد عمل کنند، سیستمهای نظارت و کنترل با ویژگیهای زیر مورد نیاز است:
- می تواند به طور انعطاف پذیر تغییرات نظارتی در موضوعات نظارتی و مقادیر حد را تطبیق دهد
- نقاط نظارت و کنترل را می توان به راحتی در هر مرحله از فرآیند اضافه کرد
- سیستم نظارت و کنترل می تواند در زمان واقعی با شرایط اضطراری مانند تخلیه پساب های سمی به رودخانه در یک مکان دور دست مقابله کند.
- به طور یکپارچه با یک سیستم نظارت و کنترل متمرکز ادغام می شود و امکان ادغام فرآیندهای ابزار و تولید را فراهم می کند.
- می تواند با قابلیت اطمینان و پایداری بالا برای مدت زمان طولانی کار کند
پلی الکترولیت ها – عوامل لخته سازی
پلی الکترولیت ها لخته های شیمیایی هستند که در تصفیه آب استفاده می شوند. آنها عمدتاً در مرحله انعقاد-لخته سازی و در تهویه/ضخیم شدن خط لجن عمل می کنند. پلی الکترولیت ها در زمینه هایی مانند تصفیه آب به عنوان عوامل لخته سازی ، در دوغاب های سرامیکی به عنوان عوامل پخش کننده و در مخلوط های بتن به عنوان روان کننده های فوق العاده کاربرد زیادی دارند.
پلی الکترولیت ها پلیمرهای آلی با زنجیره بلند هستند که اغلب دارای وزن مولکولی بیش از یک میلیون هستند و منشا طبیعی یا مصنوعی دارند. اصطلاح “پلی الکترولیت” برای شامل آن دسته از پلیمرهایی معرفی شد که با مکانیزم تولید یون می توانند به یک مولکول پلیمری با بارهای الکتریکی در طول آن تبدیل شوند. بارهای الکتریکی از وجود گروه های عاملی قابل یونیزاسیون در طول زنجیره پلیمری ناشی می شود. بنابراین پلیالکترولیتها الکترولیتهای پلیمری هستند، یعنی دارای ویژگیهای پلیمرها و الکترولیتها هستند.
پلی الکترولیت های تجاری مورد استفاده در تجمع مواد معلق محلول در آب هستند. آنها ممکن است به شکل های دانه ای، به صورت پودر یا مایعات بسیار چسبناک باشند. تمام پلی الکترولیت های موجود در صورت نگهداری در یک بازه زمانی مشخص تمایل به تخریب دارند – برای یک محصول خاص، چنین دوره ای معمولاً توسط سازنده اعلام می شود. به طور کلی، هرچه محلول پلی الکترولیت رقیقتر باشد، تجزیه سریعتر میشود، که احتمالاً شامل شکستن زنجیرههای بلند و در نتیجه کاهش ویسکوزیته میشود.
میزان استفاده از پلی الکترولیت ها
استفاده و اهمیت پلی الکترولیت ها به سرعت در حال افزایش است. تعداد تولیدکنندگانی که این مواد را تولید می کنند نیز در حال افزایش است. پلی الکترولیت های مصنوعی کاربردهای قابل توجهی در زمینه های وسیع زیر پیدا کرده اند:
- صنایع فرآیندی
- تصفیه فاضلاب صنعتی
- تصفیه آب
- تصفیه فاضلاب خانگی
پلی الکترولیت های تجاری موجود عبارتند از: پلی دی متیل آمونیوم کلرید (PolyDADMAC)، پلی اکریلیک اسید (PAA) و پلی استایرن سولفونات. گریدهای تجاری پلی الکترولیت ها (PAAs) از شرکت Dow Chemical (Duramax، Tamol، Romax، Dowex)، Rohm and Haas (Acusol، Acumer)، BASF (Dispex®، Magnafloc®)، و Arkema (Rheoslove، Terrablend) در دسترس هستند. کاربردهای خاص پلی الکترولیت ها در صنایع فرآیندی شامل شفاف سازی آب شکر خام در صنعت قند است. جداسازی گچ از فرآیند مرطوب اسید فسفریک؛ بهبود ته نشینی در عملیات زغال شویی؛ افزایش ظرفیت ضخیم کننده در تولید سیمان فرآیند مرطوب. جداسازی ناخالصی های خاک رس از جریان های داغ بوراکس؛ بهبود کیفیت رسوب فلز در پالایش الکترولیتی یا الکترووینینگ مس و روی. بهبود عملیات غلیظ سازی در فرآوری اورانیوم و غیره. از پلی الکترولیت ها می توان برای تصفیه فاضلاب صنعتی نیز استفاده کرد. مبارزه با آلودگی رودخانه ها روز به روز شدیدتر می شود و صنایع به تمام کمک هایی که می توانند دریافت کنند نیاز دارند. پلی الکترولیت ها در حال تبدیل شدن به یک عامل مهم فزاینده در حل این مسائل آلودگی هستند. در آینده پلی الکترولیت ها تاثیر بیشتری بر تصفیه فاضلاب صنعتی نسبت به تصفیه فاضلاب شهری خواهند داشت. این ممکن است به این دلیل باشد که تصفیه خانه های فاضلاب صنعتی مانند تصفیه خانه های فاضلاب شهری دارای محدودیت هایی نیستند. به این ترتیب، طراحان تصفیه خانه پسماند صنعتی ممکن است بیشتر بر کاهش هزینه های کلی تصفیه خانه متمرکز شوند تا اینکه آیا این صرفه جویی ها ناشی از سرمایه گذاری های سرمایه ای یا هزینه های عملیاتی است.
سیستم های آماده سازی و دوزینگ
پلی آکریل آمیدها پلیمرهایی با وزن مولکولی بسیار بالا هستند که به عنوان لخته ساز استفاده می شوند. این پلیمرها عمدتاً به صورت پودر یا امولسیون در دسترس هستند. آنها می توانند آنیونی یا کاتیونی باشند. عیب اصلی لخته سازی با پلیمرها پنجره لخته سازی بسیار کوچک است که خطر تعلیق مجدد ذرات با افزایش دوزهای کمی را به همراه دارد.
برخی از این محصولات به شکل محلولهای بسیار چسبناک (5000 تا 10000 سانتیپوایز) وجود دارند که میتوان آنها را با رقت ثانویه در تحویل پمپ تغذیه پمپ کرد.
فرآیند آماده سازی بر اساس سه مرحله است: انحلال، بلوغ و انتقال.
- انحلال . پلیمر با هم زدن آهسته مرطوب شده و حل می شود و به همگن شدن محلول کمک می کند.
- محلول در هم زدن مداوم و آهسته نگه داشته می شود.
- پروب های سطح به گونه ای عمل می کنند که محلول را می توان به طور خودکار به درمان لانه دوز کرد.
با اتوماسیون، مشتری میتواند از مداخلات دستی و همچنین اشتباهات هنگام دوز کردن محصول جلوگیری کند. این تجهیزات موفق می شود پلی الکترولیت های پودری را در محلول ادغام کند تا پراکندگی و عملکرد صحیح آنها را در فرآیند تصفیه آب به دست آورد.
محلول های پلی الکترولیت بسیار چسبناک هستند و اغلب فقط دوزهای بسیار کمی مورد نیاز است. بنابراین ضروری است که تلاطم کافی در نقطه دوز وجود داشته باشد تا از اختلاط سریع و کامل مقدار کمی از معرف با جریان اصلی آب اطمینان حاصل شود. محلول های پلی الکترولیت رقیق راحت تر از محلول های غلیظ در جریان پخش می شوند، اما باید تعادل برقرار شود در غیر این صورت حجم محلول پلی الکترولیت اضافه شده نسبت قابل توجهی به جریان خواهد بود.
واحد آماده سازی خودکار: https://www.keiken-engineering.com/en/polyelectrolyte-preparation-equipment/
واحد آماده سازی خودکار (مرجع: مهندسی Keiken)
رقیق سازی در خط
به منظور تضمین اثربخشی پلیمر، تقریباً همیشه لازم است محلول تهیه شده رقیق شود تا بتوان به پراکندگی یکنواخت پلیمر در آب یا لجن منعقد شده قبلی دست یافت. بنابراین، این رقت به ویسکوزیته پلیمر و لجن و انرژی اختلاط اعمال شده به سیستم بستگی دارد. در نتیجه، سطوح رقت هدف زیر اعمال خواهد شد:
- 5 تا 1 گرم · L -1 در تصفیه لجن.
- 02 تا 0.1 گرم · L –1 در شفاف سازی.
این رقیق سازی در خط در تحویل پمپ توزیع انجام می شود. این محلول به کارخانه فاضلاب پمپ می شود، محلول برای ته نشینی/انعقاد جامدات در فاضلاب استفاده می شود. هنگامی که غلظت پلی الکترولیت اشتباه باشد، آب زباله می تواند آزاد شود که می تواند منجر به جریمه شود.
برای تعیین غلظت، روشهای آزمایشی و آزمایشگاهی در مقیاس رومیزی وجود دارد:
- برای آزمایش
- تست زهکشی گرانشی
- تست خردکن
با این حال، این روش ها آفلاین و دست و پا گیر هستند. آنها از اپراتورها می خواهند که نمونه ای از مایع را جمع آوری کنند، آنها را به طور جداگانه تجزیه و تحلیل کنند و سپس تصمیم گیری در مورد فرآیند بگیرند. در مقایسه، دستگاههای درون خطی که میتوانند ویژگیهای مخلوط را نشان دهند و دوزهای تصحیح شده خودکار را ایجاد کنند، بسیار کارآمدتر، مولدتر بوده و با دوز دقیق، مصرف کلی پلیمر را کاهش میدهند.
سیستم های آماده سازی پلیمر (مرجع: PolySys CSL توسط Kozegho)
ویسکوزیته – نشانگر کارایی محلول پلیمری
پلیمر به سه شکل مختلف وجود دارد – پلیمر خشک، محلول (ماننیچ) و پلیمر امولسیونی. بیشتر پلیمرهای مورد استفاده در صنایع فاضلاب بر پایه آکریل آمید هستند و اغلب PAAM (پلی آکریل آمید) نامیده می شوند.
پلیمرهای امولسیونی مورد استفاده برای فرآیندهای جداسازی جامدات هیدرولیز شده، وزن مولکولی بالا و ویسکوزیته بسیار بالایی دارند. یکی از مهمترین ویژگیهای پلیمرهای امولسیونی، سیال بودن و ژلهای پلیمری در ابعاد میکرون است که اپراتورها را قادر میسازد تا از سیستمهای ترکیبی/خوراکی پلیمری درون خطی استفاده کنند. آنها از ژل های پلیمری امولسیون شده در روغن هیدروکربن 30 درصد تشکیل شده اند. بسته به محتوای آب در ژل های پلیمری، پلیمر فعال در پلیمر امولسیونی از 20٪ تا 55٪ متغیر است. بنابراین، هزینه پلیمرهای امولسیونی بیشتر از پلیمر خشک بر اساس هر پوند است. پلیمری که به یک سایت تحویل داده می شود، “تمیز” است و شامل آب، روغن، سورفکتانت ها و پلیمر فعال است. با این حال، محتوای فعال بخشی از امولسیون است که در واقع جامدات را در فرآیندهای پایین دستی شرایط می دهد و این محتوای فعال است که باید هنگام ارزیابی دوزهای پلیمری مناسب برای سیستم های پردازش جامد در نظر گرفته شود. پلیمرهای امولسیونی را می توان در درام های کوچک 55 گالن، توت های 270 گالن یا بارهای تانکر 4000 تا 5000 گالن تحویل داد.
مفهوم اختلاط دو مرحله ای در فرآیند ساخت پلیمر به خوبی تثبیت شده است.
- مرحله اول: اختلاط با انرژی بسیار بالا در مرحله خیس شدن اولیه برای جلوگیری از تشکیل “چشم ماهی”.
- مرحله دوم: اختلاط کم انرژی برای به حداقل رساندن آسیب رساندن به مولکولهای پلیمری که از ژل/ذرات پلیمری خارج میشوند. زمان اقامت بسیار طولانی تری برای مرحله دوم نسبت به مرحله اول مورد نیاز است.
مقدار اصطکاک که با نیروی مقاومت در برابر جریانی که در آن لایههای موازی نسبت به یکدیگر سرعت واحد دارند اندازهگیری میشود. برگه اطلاعات تامین کننده پلیمر نقطه شروعی برای فاکتور بحرانی ویسکوزیته برای کارایی پلیمر فراهم می کند.
ویسکوزیته در مقابل زمان اختلاط در آماده سازی پلی الکترولیت
وابستگی غلظت ویسکوزیته
چگونه اتوماسیون ویسکوزیته در واحدهای اختلاط پلیمری به تصفیه خانههای آب ارزش میافزاید
- کنترل / ابزار دقیق دوز پلیمری را برای تجهیزات سیستم پلیمری کهنه ارائه کنید
- دسترسی به تجهیزات O&M، افزونگی و انعطاف پذیری عملیاتی را بهبود بخشید
- مصرف انرژی کمتر
- کاهش مصرف کلی پلیمر و صرفه جویی در هزینه
- حفظ غلظت کیک و جذب مواد جامد (کمتر از 200 قسمت در میلیون (ppm) تا بازیابی مواد مغذی
راه حل های Rheonics برای سیستم های دوز پلی الکترولیت در تصفیه فاضلاب
اندازهگیری و کنترل گرانروی درون خطی خودکار برای کنترل ویسکوزیته در طول فرآیند تولید و اطمینان از مطابقت کامل ویژگیهای حیاتی با الزامات در چندین دسته، بدون نیاز به تکیه بر روشهای اندازهگیری آفلاین و تکنیکهای نمونهبرداری، حیاتی است. Rheonics راه حل های زیر را برای کنترل و بهینه سازی فرآیند ارائه می دهد:
ویسکوزیته و دانسیته متر
- در خط اندازهگیریهای ویسکوزیته : Rheonics SRV یک دستگاه اندازهگیری ویسکوزیته با طیف وسیعی است که قادر به تشخیص تغییرات ویسکوزیته در هر جریان فرآیندی در زمان واقعی است.
- درون خطی اندازه گیری ویسکوزیته و چگالی : Rheonics SRD یک ابزار اندازه گیری همزمان چگالی و ویسکوزیته در خط است. اگر اندازهگیری چگالی برای عملیات شما مهم است، SRD بهترین حسگر برای برآوردن نیازهای شما است، با قابلیتهای عملیاتی مشابه SRV همراه با اندازهگیریهای دقیق چگالی.
یکپارچه و کلید در دست کیفیت مدیریت
Rheonics یک راه حل یکپارچه برای مدیریت کیفیت ارائه می دهد که از موارد زیر تشکیل شده است:
- درون خطی اندازهگیریهای ویسکوزیته : Rheonics’ SRV – یک دستگاه اندازهگیری ویسکوزیته در محدوده وسیع با اندازهگیری دمای سیال داخلی
- مانیتور فرآیند Rheonics : یک کنترلر ردیابی پیش بینی پیشرفته برای نظارت و کنترل در تغییرات زمان واقعی شرایط فرآیند
- Rheonics RheoPulse با خودکار d osing : یک سیستم خودمختار سطح 4 که هیچ گونه مصالحه ای را با محدودیت های تعیین شده ویسکوزیته تضمین نمی کند و به طور خودکار دریچه های بای پس یا پمپ ها را برای دوز تطبیقی اجزای مخلوط فعال می کند.
سنسور SRV در خط قرار دارد، بنابراین به طور مداوم ویسکوزیته (و چگالی در مورد SRD) را اندازه گیری می کند. هشدارها را می توان برای اطلاع دادن به اپراتور از اقدامات لازم پیکربندی کرد یا کل فرآیند مدیریت را می توان با RPTC ( کنترل کننده ردیابی پیش بینی کننده Rheonics ) به طور کامل خودکار کرد. استفاده از SRV در خط فرآیند تولید، منجر به بهبود بهره وری، حاشیه سود و دستیابی به انطباق با مقررات می شود. سنسورهای Rheonics دارای یک فرم فشرده برای نصب OEM ساده و مقاوم سازی هستند. آنها نیاز به تعمیر و نگهداری یا پیکربندی مجدد صفر دارند. سنسورها بدون نیاز به محفظه های خاص، مهر و موم لاستیکی یا حفاظت مکانیکی، نتایج دقیق و قابل تکرار را بدون توجه به نحوه و مکان نصب شده ارائه می دهند. SRV و SRD بدون استفاده از مواد مصرفی و بدون نیاز به کالیبراسیون مجدد بسیار آسان هستند و در نتیجه هزینههای بسیار پایینی در طول عمر دارند.
هنگامی که محیط فرآیند ایجاد شد، معمولاً تلاش کمی برای حفظ یکپارچگی سیستم ها لازم است – اپراتورها می توانند به کنترل دقیق با راه حل مدیریت کیفیت تولید Rheonics اعتماد کنند.
مزیت Rheonics
فرم فشرده، بدون قطعات متحرک و بدون نیاز به تعمیر و نگهداری
SRV و SRD Rheonics دارای فرم فاکتور بسیار کمی برای نصب OEM ساده و مقاوم سازی هستند. آنها یکپارچه سازی آسان را در هر جریان فرآیندی امکان پذیر می کنند. آنها به راحتی تمیز می شوند و نیازی به تعمیر و نگهداری یا پیکربندی مجدد ندارند. آنها دارای ردپای کوچکی هستند که امکان نصب Inline را در هر خط فرآیندی فراهم می کند و از هرگونه فضای اضافی یا نیاز آداپتور اجتناب می کند.
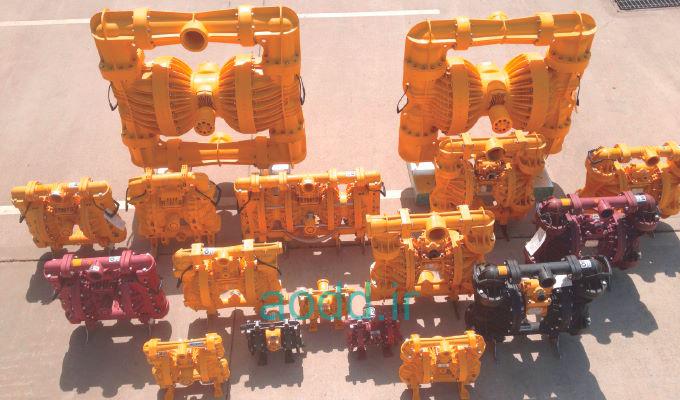
پایداری بالا و غیر حساس به شرایط نصب: هر گونه پیکربندی ممکن است
Rheonics SRV و SRD از تشدید کننده هم محوری منحصربهفرد استفاده میکنند که در آن دو انتهای حسگرها در جهت مخالف میپیچند و گشتاورهای واکنش را در محل نصب آنها خنثی میکنند و از این رو آنها را به شرایط نصب و سرعت جریان کاملاً غیر حساس میکنند. عنصر حسگر مستقیماً در سیال قرار می گیرد، بدون نیاز به محفظه خاص یا قفس محافظ.
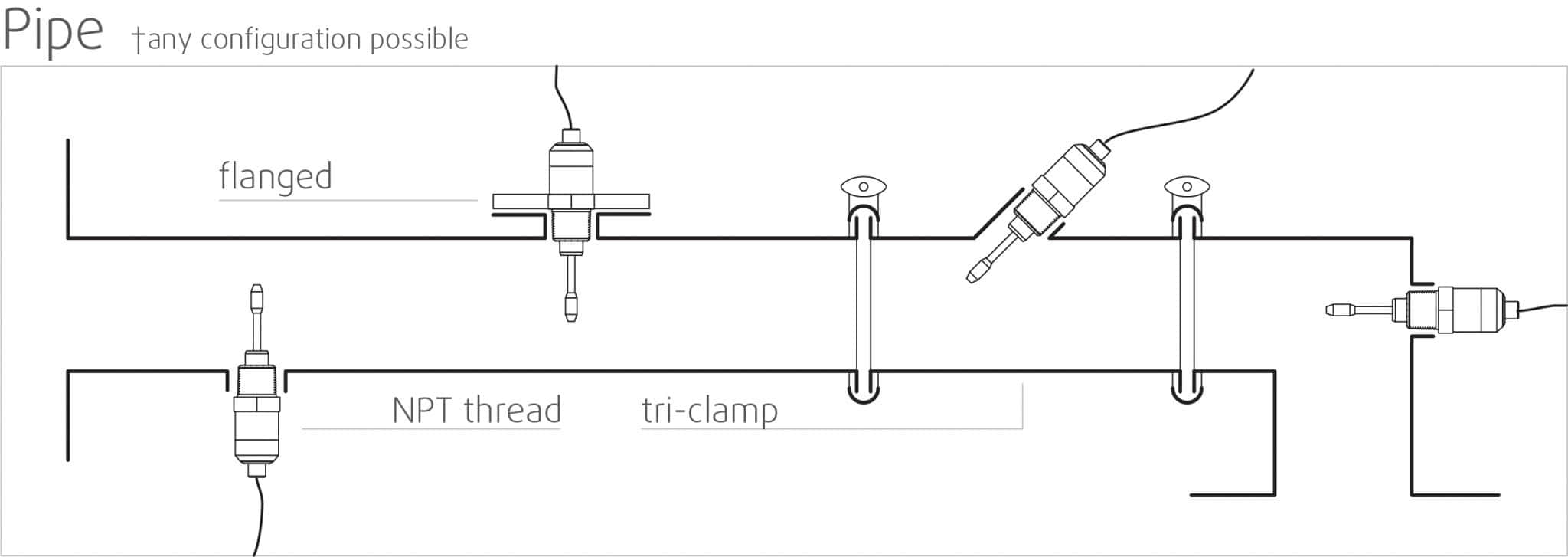
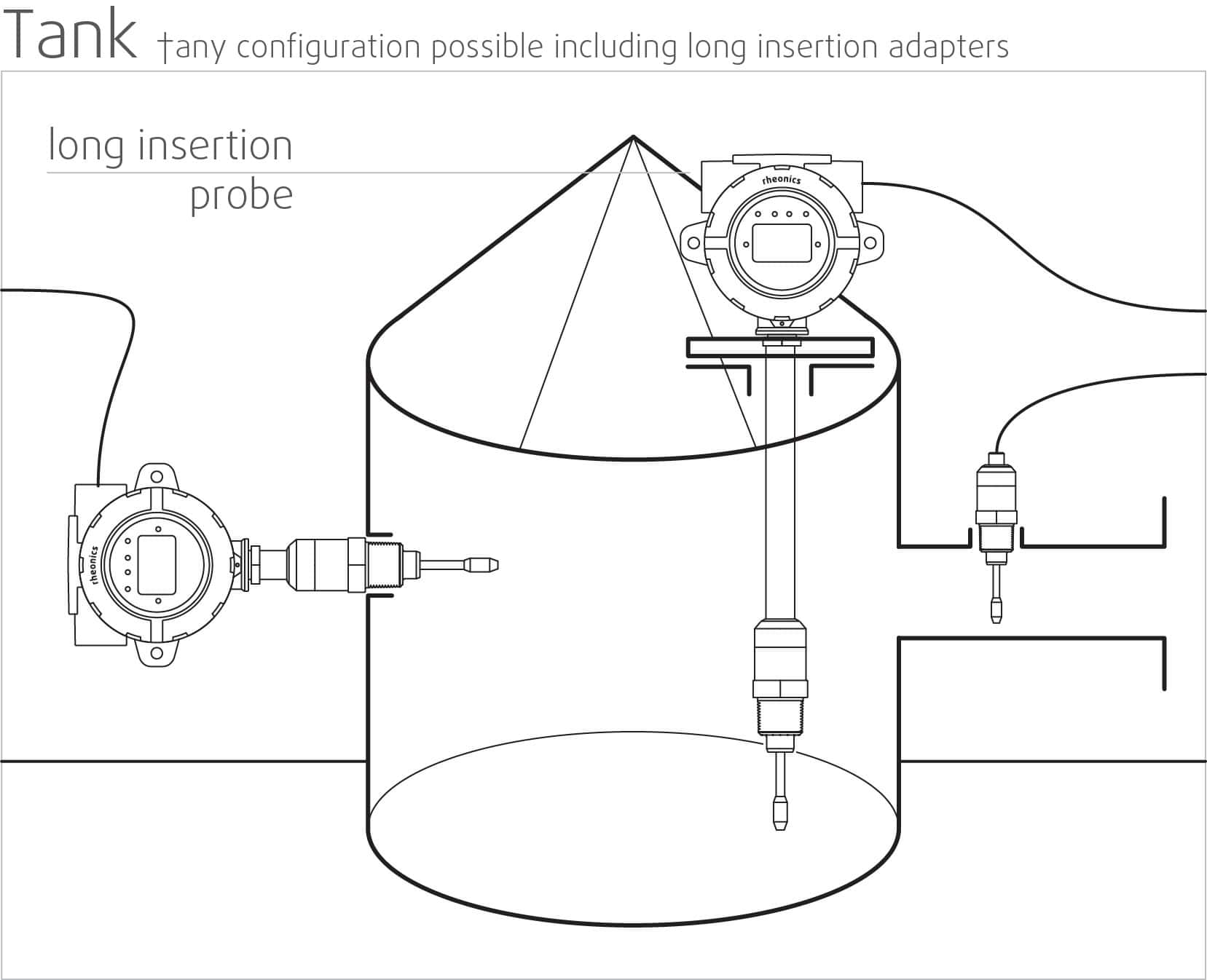
بازخوانی دقیق فوری کیفیت تولید – نمای کلی سیستم و کنترل پیش بینی
نرم افزار Rheonics قدرتمند، شهودی و برای استفاده راحت است. سیال فرآیند بیدرنگ را می توان بر روی IPC یکپارچه یا یک کامپیوتر خارجی نظارت کرد. چندین حسگر پراکنده در سراسر کارخانه از یک داشبورد مدیریت می شوند. بدون تاثیر ضربان فشار ناشی از پمپاژ بر عملکرد سنسور یا دقت اندازه گیری. بدون اثر لرزش
اندازه گیری های درون خطی، هیچ خط بای پس مورد نیاز نیست
برای انجام اندازه گیری ویسکوزیته (و چگالی) در زمان واقعی، سنسور را مستقیماً در جریان فرآیند خود نصب کنید. هیچ خط بای پس مورد نیاز نیست: سنسور را می توان در خط غوطه ور کرد. سرعت جریان و ارتعاشات بر ثبات و دقت اندازه گیری تأثیر نمی گذارد.
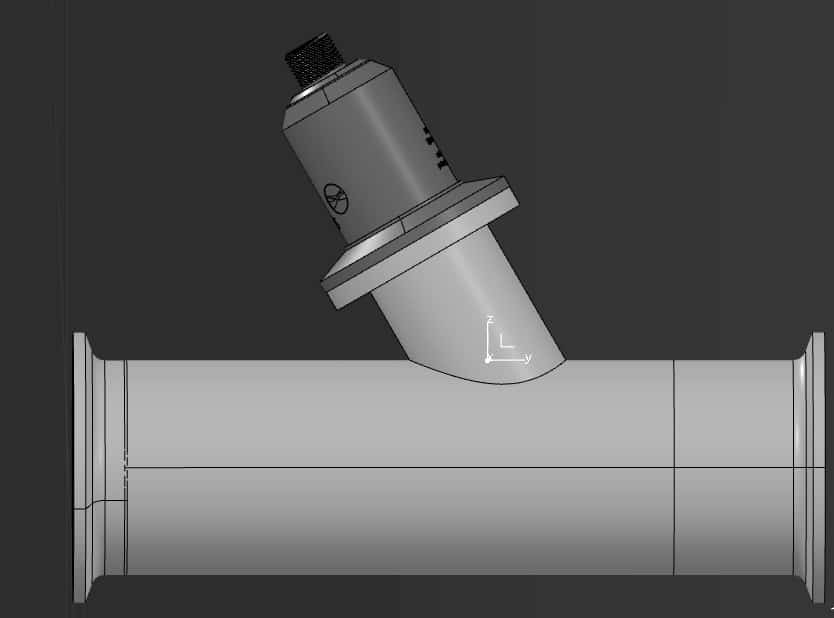
نصب آسان و بدون نیاز به پیکربندی/کالیبراسیون مجدد – تعمیر و نگهداری/زمان خرابی صفر
در صورت بعید بودن سنسور آسیب دیده، سنسورها را بدون تعویض یا برنامه ریزی مجدد وسایل الکترونیکی تعویض کنید. جایگزینی کشویی برای سنسور و لوازم الکترونیکی بدون هیچ گونه به روز رسانی سیستم عامل یا تغییر کالیبراسیون. نصب آسان. با اتصالات فرآیند استاندارد و سفارشی مانند NPT، Tri-Clamp، DIN 11851، Flange، Varinline و سایر اتصالات بهداشتی و بهداشتی موجود است. بدون اتاقک خاص به راحتی برای تمیز کردن یا بازرسی برداشته می شود. SRV همچنین با اتصال DIN11851 و سه گیره برای نصب و جداسازی آسان موجود است. پروبهای SRV برای تمیز کردن در محل (CIP) مهر و موم شدهاند و از شستشوی فشار بالا با کانکتورهای IP69K M12 پشتیبانی میکنند.
مصرف برق کم
منبع تغذیه 24 ولت DC با جریان کمتر از 0.1 آمپر در طول کارکرد عادی.
زمان پاسخ سریع و ویسکوزیته جبران شده دما
الکترونیک فوق سریع و قوی، همراه با مدل های محاسباتی جامع، دستگاه های Rheonics را به یکی از سریع ترین، همه کاره ترین و دقیق ترین در صنعت تبدیل کرده است. SRV و SRD هر ثانیه اندازه گیری ویسکوزیته (و چگالی SRD) را در زمان واقعی و دقیق انجام می دهند و تحت تأثیر تغییرات نرخ جریان نیستند!
قابلیت های عملیاتی گسترده
ابزارهای Rheonics برای اندازه گیری در سخت ترین شرایط ساخته شده اند.
SRV موجود است : با گسترده ترین محدوده عملیاتی در بازار برای ویسکومتر فرآیند درون خطی
- محدوده فشار تا 5000 psi
- محدوده دما از -40 تا 200 درجه سانتیگراد
- محدوده ویسکوزیته: 0.5 cP تا 50000 cP (و بالاتر)
SRD: تک ابزار، سه کاره – ویسکوزیته، دما و چگالی
SRD Rheonics یک محصول منحصر به فرد است که جایگزین سه ابزار مختلف برای اندازه گیری ویسکوزیته، چگالی و دما می شود. دشواری مکان یابی سه ابزار مختلف را از بین می برد و اندازه گیری های بسیار دقیق و قابل تکرار را در سخت ترین شرایط ارائه می دهد.
طراحی و فناوری سنسور برتر
الکترونیک پیچیده و ثبت شده مغز این حسگرها است. SRV و SRD با اتصالات فرآیند استاندارد صنعتی مانند NPT ¾ اینچ، DIN 11851، فلنج و گیره سهگانه در دسترس هستند که به اپراتورها اجازه میدهد حسگر دمای موجود را در خط فرآیند خود با SRV/SRD جایگزین کنند که علاوه بر ویسکوزیته، اطلاعات سیال فرآیند بسیار ارزشمند و قابل عملی را ارائه میدهد. اندازه گیری دقیق دما با استفاده از Pt1000 داخلی (DIN EN 60751 Class AA, A, B موجود است).
وسایل الکترونیکی متناسب با نیاز شما ساخته شده است
حسگر الکترونیکی که هم در محفظه فرستنده و هم در پایه ریلی DIN با فاکتور کوچک موجود است، امکان ادغام آسان در خطوط فرآیند و داخل کابینت تجهیزات ماشینها را فراهم میکند.
گزینه های الکترونیک و ارتباطات را کاوش کنید
آسان برای ادغام
چندین روش ارتباطی آنالوگ و دیجیتال اجرا شده در الکترونیک حسگرها، اتصال به PLC صنعتی و سیستم های کنترل را ساده و ساده می کند.
مطابقت با ATEX و IECEx
Rheonics حسگرهای ذاتاً ایمن ارائه می دهد که توسط ATEX و IECEx برای استفاده در محیط های خطرناک تأیید شده اند. این حسگرها با الزامات بهداشتی و ایمنی ضروری مربوط به طراحی و ساخت تجهیزات و سیستم های حفاظتی در نظر گرفته شده برای استفاده در جوهای بالقوه انفجاری مطابقت دارند.
گواهینامه های ذاتاً ایمن و ضد انفجار که توسط Rheonics ارائه می شود همچنین امکان سفارشی سازی حسگر موجود را فراهم می کند و به مشتریان ما امکان می دهد از زمان و هزینه های مرتبط با شناسایی و آزمایش یک جایگزین اجتناب کنند. حسگرهای سفارشی را می توان برای برنامه هایی که به یک واحد تا هزاران واحد نیاز دارند ارائه کرد. با زمان سرب هفته ها در مقابل ماه ها.
Rheonics SRV & SRD هر دو دارای گواهینامه ATEX و IECEx هستند.
دارای گواهینامه ATEX (2014/34/EU).
حسگرهای ایمن ذاتی دارای گواهینامه ATEX Rheonics با دستورالعمل ATEX 2014/34/EU مطابقت دارند و دارای گواهینامه ایمنی ذاتی به Ex ia هستند. دستورالعمل ATEX حداقل و الزامات ضروری مربوط به سلامت و ایمنی را برای محافظت از کارگران شاغل در جوهای خطرناک مشخص می کند.
سنسورهای Rheonics دارای گواهی ATEX برای استفاده در اروپا و بینالمللی شناخته شدهاند. تمام قطعات دارای گواهی ATEX با علامت “CE” برای نشان دادن انطباق علامت گذاری شده اند.
دارای گواهینامه IECEx
حسگرهای ذاتا ایمن Rheonics توسط IECEx، کمیسیون بین المللی الکتروتکنیکی برای گواهی استانداردهای مربوط به تجهیزات برای استفاده در جوهای انفجاری تایید شده اند.
این یک گواهینامه بین المللی است که انطباق ایمنی را برای استفاده در مناطق خطرناک تضمین می کند. سنسورهای Rheonics دارای گواهینامه ایمنی ذاتی تا Ex i هستند.